The future looks bright for Australia's mining and industrial sectors, with exploration and production expected to ramp up over the rest of 2020. Bloomberg News reported that several leading mining companies plan to increase spending on their Australia-based operations to capitalise on the rising prices for precious metals and materials such as gold, coal and iron.
That's great news for Australia's mining industry, which has seen exploration budgets and drilling activity drop in recent years, to say nothing of the disruptive impact of the COVID-19 pandemic. With a major rebound on the horizon, mining operators need to ensure their infrastructure and equipment are able to keep up with the expected increase in demand.
Outdated machinery could be a significant liability for mining companies, increasing the risk of equipment breakdown and production stoppages. Rather than replacing legacy equipment outright at a steep cost, operators should consider retrofitting existing machinery to better meet their mining needs for the foreseeable future.
Maintain high productivity at a lower cost
Equipment malfunction and failure is the worst-case scenario when relying on legacy machinery, but outdated conveyor systems, weigh feeders and other critical mining tools can cost companies a lot of money even when they're running at full capacity. They may not be able to support mining operations at the scale and speed required of them to meet current demand. Wear and tear will reduce the effectiveness of any piece of equipment if given enough time, and that's especially true with machinery placed in industrial environments.
Any drop in production means companies are missing out on potential revenue. If they don't address operability issues with their outdated equipment, those losses will continue to pile up and hurt their bottom line.
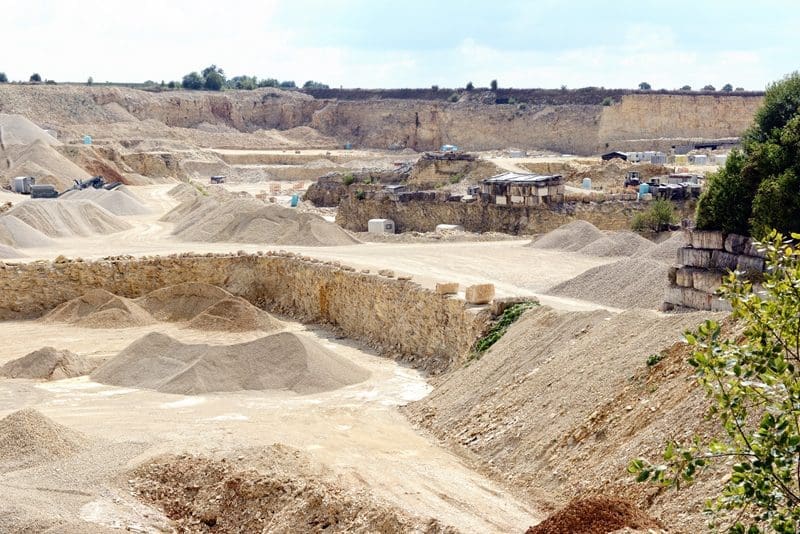
Replacing old machinery and tools is not always a cost-effective option. Any industrial equipment purchase will require a high initial investment, and companies may not have enough capital available at this moment to make that change. In addition, replacing critical equipment can be very time-consuming, requiring days – maybe even weeks – to complete. Every hour that goes by with machinery offline is lost production time.
Retrofitting can provide a better alternative that minimises downtime, increasing productivity and positioning sites to meet future demand.
Modernise legacy equipment with the latest technology
From measuring harvested minerals and sorting out unwanted particulates to processing raw materials and transporting finished products, precision is key in the mining industry. State-of-the-art calibration and measurement tools help site operators ensure that the correct volume and combination of materials is present at every step of the process.
Retrofitting legacy equipment with the latest industrial solutions, including weightometers, conveyor belt scales and weigh feeders, gives mining companies complete confidence in their production sites. Stakeholders and site operators can rest easy knowing that their essential equipment is running smoothly, meeting production demands and will continuing to perform at a high level for years to come. Contact SRO Technology today to find out more about our retrofitting services and how we can help improve your industrial operations.
Recent Comments