Production levels in a coal mine are influenced by so many factors. The elements play a big role. In addition, human error, system malfunctions and equipment problems can all weigh in to give inaccurate productivity readings. As an example, if a coal mine’s level measurement devices told managers the facility had processed 4,200 tonnes of material in a given day when it had actually produced 4,250 tonnes, this sort of inconsistency could mean thousands of dollars in unrealised revenue.
Environmental factors
Keeping nature’s influence in mind when measuring productivity output is of utmost importance. According to a report by the Australian Government Productivity Commission entitled “Productivity in the Mining Industry: Measurement and Interpretation,” variables other than technology, management, skills and work practices should be considered when determining multifactor productivity (MFP).
The input of natural resources is a main contributing factor to mining production. However, changes in resource quality are not always taken into account in standard measures of productivity. As mineral and energy deposits are depleted, the quality and accessibility of remaining reserves generally decline. Remaining deposits may be of lower grade, in more remote locations, deeper in the ground (mixed with greater impurities) and require more difficult extraction techniques. Thus, more effort is needed to produce a unit of output. This slows up as a decline in measured productivity.
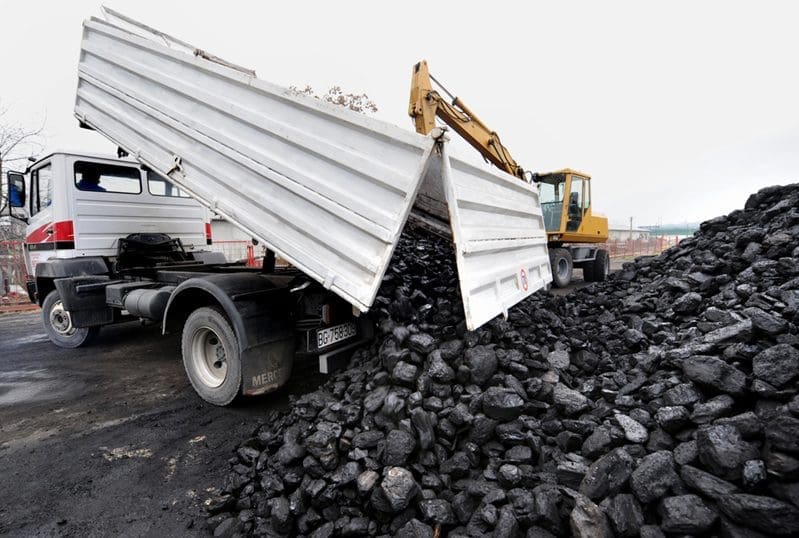
Additional influences
It’s especially important that level measurement solutions are accurate in the coal industry. Inaccurate measurements cause problems throughout the production line.
Given the adverse environments of some coal mines, it is not always easy for transmitters to provide accurate level measurements. Factors such as dust, vibrations and noise can significantly interfere with the precision of important sensors.
To combat this, a number of mine operators are opting for radar transmitters, which are unaffected by ambient influences. Ultrasonic sensors are also widely used in coal mines to monitor the flow of raw material from the moment it is cut at the face until it finally leaves the coalfield in railway wagons. These sensors can do so much: detect blocked chutes, count mine cars in and out of cages, monitor coal in bunkers and hoppers and position the mine cage for loading.
This is where SRO Technology comes in.
SRO Technology specialises in sensors for iron ore and coal mines, as well as many other industries. We’ll establish a well-structured maintenance and calibration schedule to check up on operations as necessary. As a part of our maintenance and calibration services, we audit and deliver informed recommendations as to how you can better use your sensors. Our ultimate goal is to help you establish and maintain cost-effective solutions that improve your operations. If you’d like to know more about our services, contact us at 61 2 9525 3077, or send an email to sales@srotechnology.com.
Recent Comments